First, reduce the variety of conveyors in operation generated dust, noise and emissions.
Second, the conveyor structure to meet the material handling system automation and control for single requests. As used in automated sorting post office parcel trolley conveyor
sorting operation should meet the requirements.
Third, the expansion of the use of the vertical conveyor. Developments in high temperature, low temperature, corrosive, radioactive, flammable substances in the work environment, as well
as capable of delivering hot, easy to agglomerate, explosive, viscous material conveyor.
Fourth, to large-scale development. Large transmission capacity, including large-scale, large single length and large transmission angle and other aspects. Hydraulic conveyor
length reached 440 km or more. Belt conveyor length of nearly 15 km single, and has appeared composed by a number of Taiwan Contact B two places. "
Belt Conveyor Road. "Many countries are exploring long-distance, large capacity continuous transport of materials better 90 degree turn conveyor structure.
Fifth, reduce energy consumption in order to save energy, the field of conveyor technology has become an important aspect of research. Has one ton material handling energy
consumed by one kilometer conveyor selection as one important indicator.
Airport conveyor equipment belonging to airport cargo for bagged cargo transportation, Zhengzhou Modern Automation Equipment Co., LTD airport conveyor with safety and convenience features. At the airport using the airport conveyor can greatly reduce labor intensity and improve the efficiency of freight transport system.
hot water heat exchanger
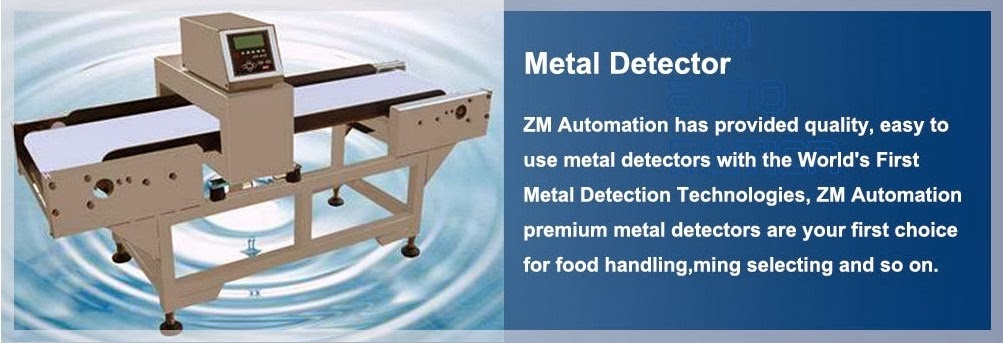
hot water heat exchanger
2013年7月31日星期三
Debugging What are the steps conveyor
First, after the installation of each device carefully debugging conveyors meet the design requirements.
Second, the reducer, moving parts corresponding filling oil.
Third, install Flat belt conveyor meet the requirements of a single device for manual work test, and debug conveyors combine action to meet the requirements.
Fourth, the electrical part of the conveyor debugging. Including the action of conventional electrical wiring and commissioning, the chain conveyor with good performance, to meet the design features and status.
Second, the reducer, moving parts corresponding filling oil.
Third, install Flat belt conveyor meet the requirements of a single device for manual work test, and debug conveyors combine action to meet the requirements.
Fourth, the electrical part of the conveyor debugging. Including the action of conventional electrical wiring and commissioning, the chain conveyor with good performance, to meet the design features and status.
2013年7月30日星期二
Screw conveyor arrangement
Usually driven by screw machine, the first part, an intermediate portion of some of the standard, the middle part matches the command shell and supporting form.In except the end
portion of the first part, the casing and each section interchangeable screw conveyor, the end of the Qing screw feeding device of materials, installation, pay attention
location.Drive consists of a planetary cycloid motor (or other gear motor) commitments, and thrust bearings installed in the holiday first mobile phone, when the material is
transported to the axial force from the suspension and chassis bearing and the first part of basic equipment generated an intermediate portion of each security
Points have been used to support the propeller shaft bearing hanging, hanging bearings with radial ball bearings (or the entire bearing) at the end, with the scroll's holiday
(sliding) bearings to support and more helical screw shaft length error, install should start from the head, order. Screw (Spiral
Conveyor manufacturers, Elevator conveyor parameter) must be installed conveyor installation accuracy in good condition or not, is one of the prerequisites for everyday use, the use of
location technologies installed must meet the following requirements: If installed on the basis of the screw conveyor at least 10 days before the official end
Installation and water into the foundation should be able to reliably transport and support to ensure that the Foundation is not too small, because the screw hangars and other
changes to ensure that occur when operating the machine curve conveyor screw stability.When enough to hang in the dust Here, from the top of the spiral gray powder
Dust outlet conveyor bottom, left, and right will be.
portion of the first part, the casing and each section interchangeable screw conveyor, the end of the Qing screw feeding device of materials, installation, pay attention
location.Drive consists of a planetary cycloid motor (or other gear motor) commitments, and thrust bearings installed in the holiday first mobile phone, when the material is
transported to the axial force from the suspension and chassis bearing and the first part of basic equipment generated an intermediate portion of each security
Points have been used to support the propeller shaft bearing hanging, hanging bearings with radial ball bearings (or the entire bearing) at the end, with the scroll's holiday
(sliding) bearings to support and more helical screw shaft length error, install should start from the head, order. Screw (Spiral
Conveyor manufacturers, Elevator conveyor parameter) must be installed conveyor installation accuracy in good condition or not, is one of the prerequisites for everyday use, the use of
location technologies installed must meet the following requirements: If installed on the basis of the screw conveyor at least 10 days before the official end
Installation and water into the foundation should be able to reliably transport and support to ensure that the Foundation is not too small, because the screw hangars and other
changes to ensure that occur when operating the machine curve conveyor screw stability.When enough to hang in the dust Here, from the top of the spiral gray powder
Dust outlet conveyor bottom, left, and right will be.
Scraper conveyor recycling Safety Measures
Scraper conveyor removal work done after the withdrawal channel, first with the scraper scraper chain removal and shipped out from the machine after loading lane, the front of
the scraper conveyor middle groove and frameworks are using the ramp through the main and auxiliary winch traction in the face direct loading transport from the wind, Lane
shipped out; after
Department of conveyors for recycling simultaneously in two stages, in order to ensure the construction safety, specially formulated the following measures.
A scraper conveyor retracement order
Scraper and scraper chain - scraper conveyor tail and the transmission unit cooling pipes and cables - scraper conveyor and transmission department head - head bent transition
slots - Central trough and cable trough
Second, dismantling, loading and bundled
1, removal scraper conveyor, you should first power lockout, and then in the head at the transition slot on the chain pinch the blade open, latching nose to tail motor
electrical power transmission, tail motor forward jog all the scraping spit plate chain and pulled the coal wall side with artificial segmentation slave Lane loading shipped
out.
2, scraper conveyor tail removed, the use of airway traction winch lifting device under the disintegration of its drive unit removed, respectively loading. Loading specific
method is the use of two inverted chain Diaozhu part two were lifting a certain height, it will push the device under loading flatbed
, Tied when bundled less than 6 per car, at least every 6 shares 8 # galvanized wire twisted tight bundle, the first with 8 # lead wire bundle fixed at the corners, and then two
Φ18.5mm rope Shengkou flower field with screws diagonally cross bundle.
3, tail transition groove and adjacent two central grooves are shipped to pull the wind carried Lane loading.
4, the above work is completed, the installation turntable road and laying work, and to prepare for disassembling the middle groove with.
5, the central groove and cable trough demolition, the first two should be removed on the coal wall side of the rack, and then remove the cable channel, the overall removal
chute every two middle pins connected dumbbell is not removable.
6, the central trough cable trays are used together with the loading ramp, the use of the main winch towing flatbed, flatbed with ramps and reliable connection, the central
framework vice traction winch loading, loading a bundle requires a good one, tied as above , tied to solid and reliable, equipment bundled
Good only after the solution out of the vice winch hook, every car requires just installed two chutes and two cable ducts.
7, after loading bundles, upon inspection no problem, remove the ramps connecting pin with flat floor, remove the auxiliary winch rope track, using the main winch upgrade to the
turntable Dogo, use winch shipped to +1170 m yard.
8, after the disintegration of the nose Belt conveyor also use loading ramps, loading and binding the same way as the central trough installed.
9, the rear conveyor recycling front, rear tail boom flapper play all the case, first the rear left side of the float coal conveyor clean, check the rear side of the conveyor
empty old roof maintenance situation, confirming that no hazards, then Check the help section catchy extended support, in the case of support intact, taking
Middle pillar, freeing recovery channel, started recycling, found after extraction roof support is not reliable, you must use the same set of specifications of the shed roof
support.
10, disassembly and recycling during the bracket must be normal for the fluid, let someone check the stent in good condition, if any leakage and other circumstances, it must be
treated immediately to prevent stent tail beam landing.
11, the rear conveyor recycling, recovery can be divided into two simultaneously (in the center bracket 60 #), or the section from top to bottom, and the lower bottom-up order
recycled.
12, tail recycling machine, you can use Wind Tunnel winch with guide wheels for recycling. The guide pulley 40T chain ring or use new wire rope Shengkou fixed at 100 # frame
tail beam column to help the closure, the 60 # 100 # rack shelves above paragraph from space to help out, drag loading to
Points classification loading away.
13, the rear Plastic belt conveyor and transmission unit, the available five tons guide chain pull operation. Slip nose section after recovery until the end of the head support recovery
is completed, the roof of the mouth under the safeguard, the use of machine Lane installed JH-14 type winch for recovery with the guide pulley, the guide pulley use
New 40T chain ring set up branches or rope cord lock closure column fixed at one side of the tail boom holder # transition machine Lane proper position, pull out the rear for
loading the machine Lane Sinotrans. Loading and bundled with the former slip.
14, recovered slipped ago, at the end of the beam 60 # frame to play at two closure column or the use of bundled 40T chain ring placed Woods car stop, prevent recovery of more
than 60 # frame when the equipment fell chute, where hung metal mesh tablets, the upper and lower sections are separated to prevent debris recovered catchy slide after slide
wounding.
15, slipped into operation after pulling equipment, wire rope shall not be someone along to work or stay, personnel must stand between the two stents observation equipment pull
operation, if the problem, immediately stop the pull operation, handle before continuing.
16, slipped into operation after pulling device, prohibited personnel entering or working in the bracket at the end of the beam. After the slide to prevent decline after the
slip joint bracket and chain not earlier dismantle, demolish one must follow the order, shipped one, dismantling and transportation to coordinate each LaYun chute not more than
two.
17, the upper and lower two recovered simultaneously, you must pull the factions hand observation equipment transport situation and must be dry by the on-site valet team and
stare unified command post personnel, on-site supervision.
18, after the completion of slipped equipment recycling, recycling shed beams and catchy single pillar in a timely manner with the old sleepers erected two "#" shaped wood crib,
then real catchy roof. In the side of the crib and the 100 # bracket tail boom cut the top line together, outside wood crib with 100 # support base front-flush. Catchy recycling
shed and a single beam
Body pillars should be inside out by stand-by trees for recycling, recycling lay supporter closure column before, strict implementation of the "first branch and then back"
principle, to be wood crib, then recovered plate girder then real prop.
the scraper conveyor middle groove and frameworks are using the ramp through the main and auxiliary winch traction in the face direct loading transport from the wind, Lane
shipped out; after
Department of conveyors for recycling simultaneously in two stages, in order to ensure the construction safety, specially formulated the following measures.
A scraper conveyor retracement order
Scraper and scraper chain - scraper conveyor tail and the transmission unit cooling pipes and cables - scraper conveyor and transmission department head - head bent transition
slots - Central trough and cable trough
Second, dismantling, loading and bundled
1, removal scraper conveyor, you should first power lockout, and then in the head at the transition slot on the chain pinch the blade open, latching nose to tail motor
electrical power transmission, tail motor forward jog all the scraping spit plate chain and pulled the coal wall side with artificial segmentation slave Lane loading shipped
out.
2, scraper conveyor tail removed, the use of airway traction winch lifting device under the disintegration of its drive unit removed, respectively loading. Loading specific
method is the use of two inverted chain Diaozhu part two were lifting a certain height, it will push the device under loading flatbed
, Tied when bundled less than 6 per car, at least every 6 shares 8 # galvanized wire twisted tight bundle, the first with 8 # lead wire bundle fixed at the corners, and then two
Φ18.5mm rope Shengkou flower field with screws diagonally cross bundle.
3, tail transition groove and adjacent two central grooves are shipped to pull the wind carried Lane loading.
4, the above work is completed, the installation turntable road and laying work, and to prepare for disassembling the middle groove with.
5, the central groove and cable trough demolition, the first two should be removed on the coal wall side of the rack, and then remove the cable channel, the overall removal
chute every two middle pins connected dumbbell is not removable.
6, the central trough cable trays are used together with the loading ramp, the use of the main winch towing flatbed, flatbed with ramps and reliable connection, the central
framework vice traction winch loading, loading a bundle requires a good one, tied as above , tied to solid and reliable, equipment bundled
Good only after the solution out of the vice winch hook, every car requires just installed two chutes and two cable ducts.
7, after loading bundles, upon inspection no problem, remove the ramps connecting pin with flat floor, remove the auxiliary winch rope track, using the main winch upgrade to the
turntable Dogo, use winch shipped to +1170 m yard.
8, after the disintegration of the nose Belt conveyor also use loading ramps, loading and binding the same way as the central trough installed.
9, the rear conveyor recycling front, rear tail boom flapper play all the case, first the rear left side of the float coal conveyor clean, check the rear side of the conveyor
empty old roof maintenance situation, confirming that no hazards, then Check the help section catchy extended support, in the case of support intact, taking
Middle pillar, freeing recovery channel, started recycling, found after extraction roof support is not reliable, you must use the same set of specifications of the shed roof
support.
10, disassembly and recycling during the bracket must be normal for the fluid, let someone check the stent in good condition, if any leakage and other circumstances, it must be
treated immediately to prevent stent tail beam landing.
11, the rear conveyor recycling, recovery can be divided into two simultaneously (in the center bracket 60 #), or the section from top to bottom, and the lower bottom-up order
recycled.
12, tail recycling machine, you can use Wind Tunnel winch with guide wheels for recycling. The guide pulley 40T chain ring or use new wire rope Shengkou fixed at 100 # frame
tail beam column to help the closure, the 60 # 100 # rack shelves above paragraph from space to help out, drag loading to
Points classification loading away.
13, the rear Plastic belt conveyor and transmission unit, the available five tons guide chain pull operation. Slip nose section after recovery until the end of the head support recovery
is completed, the roof of the mouth under the safeguard, the use of machine Lane installed JH-14 type winch for recovery with the guide pulley, the guide pulley use
New 40T chain ring set up branches or rope cord lock closure column fixed at one side of the tail boom holder # transition machine Lane proper position, pull out the rear for
loading the machine Lane Sinotrans. Loading and bundled with the former slip.
14, recovered slipped ago, at the end of the beam 60 # frame to play at two closure column or the use of bundled 40T chain ring placed Woods car stop, prevent recovery of more
than 60 # frame when the equipment fell chute, where hung metal mesh tablets, the upper and lower sections are separated to prevent debris recovered catchy slide after slide
wounding.
15, slipped into operation after pulling equipment, wire rope shall not be someone along to work or stay, personnel must stand between the two stents observation equipment pull
operation, if the problem, immediately stop the pull operation, handle before continuing.
16, slipped into operation after pulling device, prohibited personnel entering or working in the bracket at the end of the beam. After the slide to prevent decline after the
slip joint bracket and chain not earlier dismantle, demolish one must follow the order, shipped one, dismantling and transportation to coordinate each LaYun chute not more than
two.
17, the upper and lower two recovered simultaneously, you must pull the factions hand observation equipment transport situation and must be dry by the on-site valet team and
stare unified command post personnel, on-site supervision.
18, after the completion of slipped equipment recycling, recycling shed beams and catchy single pillar in a timely manner with the old sleepers erected two "#" shaped wood crib,
then real catchy roof. In the side of the crib and the 100 # bracket tail boom cut the top line together, outside wood crib with 100 # support base front-flush. Catchy recycling
shed and a single beam
Body pillars should be inside out by stand-by trees for recycling, recycling lay supporter closure column before, strict implementation of the "first branch and then back"
principle, to be wood crib, then recovered plate girder then real prop.
2013年7月29日星期一
Conveyor history and multi-faceted presentation
Conveyor history and multi-faceted presentation
In a certain line of material handling machinery continuous transport of materials, also known as continuous gravity conveyor. Conveyor can be horizontal, inclined and vertical
conveyor can also be composed space transmission line. Transmission lines are generally fixed. Conveyor conveying capacity, long distance, also in the transportation over
Simultaneously process a number of process operations, widely used.
Chinese ancient high drum dumper trucks and put water in the modern scraper bucket elevators and conveyors prototype. 17th century, began to apply ropeway transport bulk
materials. Mid-19th century, a variety of modern structural conveyor has emerged. In 1868, the band appeared in the UK lose
Sending machine. In 1887, in the United States appeared screw conveyor. In 1905, appeared in Switzerland steel belt conveyor. In 1906, in the United Kingdom and Germany appeared
inertia conveyor. After conveyors manufactured by mechanical, electrical, chemical and metallurgical industries impact of technological advances, constantly
Improved gradually from the workshop to complete the development of the internal transport within the enterprise to accomplish, even between enterprises between cities material
handling, mechanized and automated material handling systems become an indispensable component.
Classification and structure of the conveyor is generally based on whether the pulling elements to be classified.
① conveyor having a traction member generally include traction, bearing components, drive means, tensioning means, such as redirecting means and the support member. Tractor
parts used to pass traction, can be used conveyor, drag chain or rope. Order to put the material carrying member, a hopper, bracket, or
Spreader, carrying personnel have rung. Conveyor drive unit to be power, generally consists of motor, reducer and brake (stopper) and other components. Tensioning devices
generally have two kinds of screw and a hammer, can maintain a certain tension pulling pieces and dip, in order to ensure the normal conveyor
Operation. Supporting member for supporting the tractor parts or carrying member, can be idlers, rollers, etc. A conveyor having a traction member structure is characterized by:
the material to be transported to the traction member mounted on the bearing member are joined together, or in directly mounted on the pulling element (such as belt), the
traction member around
Over the drum or sprocket connected end to end, including the transportation of materials to form branches and non-load transportation of materials unloaded branch closed loop,
continuous motion using the pulling element conveying materials. Such a wide range of conveyors, are: belt conveyors, slat conveyors, trolley conveyors
Machine, escalators, moving walkways, scraper conveyor, buried scraper conveyor, bucket conveyor, bucket elevator, overhead conveyors and overhead lifts, etc. (see figure).
② conveyor without pulling element different structure and composition, working member for transporting the material is not the same. Their structure is characterized by: the
use of rotational movement of the work member or reciprocating motion, or by the medium flowing in a pipe conveying the material forward. Roller conveyor
The working member of a series of rollers, the roller rotates to deliver material. Working member of the spiral screw conveyor, spiral chute rotates in order to push the
material along the trough. Vibrating conveyor working member is trough, the trough is reciprocated to convey disposed therein
Materials. Pneumatic conveying equipment, hydraulic conveying device and the container-type devices to piped gas or liquid as the medium in the pipeline transportation of
materials.
Most uses electric drive conveyor, there is also an internal combustion engine driven, pneumatic or hydraulic driven.
The main parameters are generally based on the requirements of material handling systems, material handling location of a variety of conditions, the production process and
material characteristics to determine the main parameters. ① Transmission capacity: conveyor transport capacity per unit time is the amount of material transported. In transport bulk materials, transportation of materials per hour mass or volume calculations; during transportation into items, the number of pieces
per hour transport calculations. ② Conveyor speed: increase transmission speed can increase transmission capacity. In order to make conveyor belt retractor
Cited pieces and feed length is large, the conveying speed increasing day by day. But high-speed operation of the belt should pay attention to vibration, noise, and start
braking and other issues. For chains as traction element conveyor, conveyor speed should not be too large to prevent increased dynamic loads. Work simultaneously
Arts operated conveyors, conveyor speed production process requirements should be determined. ③ component size: scantling including conveyor belt width, belt width, hopper
volume, pipe diameter and vessel size. These have a direct impact scantlings conveyor conveying capacity. ④ lose
Delivery length and angle: transfer line length and inclination conveyor directly affect the size of the total resistance and the power required.
Development trend towards the development of the conveyor are: ① continue to large-scale development. Large transmission capacity, including large-scale, large single length
and large transmission angle and other aspects. Hydraulic conveyor length reached 440 km or more. Belt conveyor length of nearly 15 km single,
And has appeared composed by a number of Taiwan Contact B two places "belt conveyor path." Many countries are exploring long-distance, large-capacity transport of materials
better continuous conveyor structure. ② to expand the use of the conveyor. Developments in high temperature, low temperature, corrosive, radioactive
Sex, flammable substances in the work environment, as well as capable of delivering fiery, explosive, Pellet, sticky material conveyor. ③ the conveyor structure to meet the
automated material handling system to control stand-alone asked for. As used in automated sorting post office parcel trolley conveyor
Sorting machine should be able to meet the requirements of such action. ④ reduce energy consumption in order to save energy, the field of conveyor technology has become an
important aspect of research. Has one ton material handling energy consumed by one kilometer conveyor selection as one important indicator. ⑤ reduce all kinds of conveyors
Generated during operation of dust, noise and emissions.
In a certain line of material handling machinery continuous transport of materials, also known as continuous gravity conveyor. Conveyor can be horizontal, inclined and vertical
conveyor can also be composed space transmission line. Transmission lines are generally fixed. Conveyor conveying capacity, long distance, also in the transportation over
Simultaneously process a number of process operations, widely used.
Chinese ancient high drum dumper trucks and put water in the modern scraper bucket elevators and conveyors prototype. 17th century, began to apply ropeway transport bulk
materials. Mid-19th century, a variety of modern structural conveyor has emerged. In 1868, the band appeared in the UK lose
Sending machine. In 1887, in the United States appeared screw conveyor. In 1905, appeared in Switzerland steel belt conveyor. In 1906, in the United Kingdom and Germany appeared
inertia conveyor. After conveyors manufactured by mechanical, electrical, chemical and metallurgical industries impact of technological advances, constantly
Improved gradually from the workshop to complete the development of the internal transport within the enterprise to accomplish, even between enterprises between cities material
handling, mechanized and automated material handling systems become an indispensable component.
Classification and structure of the conveyor is generally based on whether the pulling elements to be classified.
① conveyor having a traction member generally include traction, bearing components, drive means, tensioning means, such as redirecting means and the support member. Tractor
parts used to pass traction, can be used conveyor, drag chain or rope. Order to put the material carrying member, a hopper, bracket, or
Spreader, carrying personnel have rung. Conveyor drive unit to be power, generally consists of motor, reducer and brake (stopper) and other components. Tensioning devices
generally have two kinds of screw and a hammer, can maintain a certain tension pulling pieces and dip, in order to ensure the normal conveyor
Operation. Supporting member for supporting the tractor parts or carrying member, can be idlers, rollers, etc. A conveyor having a traction member structure is characterized by:
the material to be transported to the traction member mounted on the bearing member are joined together, or in directly mounted on the pulling element (such as belt), the
traction member around
Over the drum or sprocket connected end to end, including the transportation of materials to form branches and non-load transportation of materials unloaded branch closed loop,
continuous motion using the pulling element conveying materials. Such a wide range of conveyors, are: belt conveyors, slat conveyors, trolley conveyors
Machine, escalators, moving walkways, scraper conveyor, buried scraper conveyor, bucket conveyor, bucket elevator, overhead conveyors and overhead lifts, etc. (see figure).
② conveyor without pulling element different structure and composition, working member for transporting the material is not the same. Their structure is characterized by: the
use of rotational movement of the work member or reciprocating motion, or by the medium flowing in a pipe conveying the material forward. Roller conveyor
The working member of a series of rollers, the roller rotates to deliver material. Working member of the spiral screw conveyor, spiral chute rotates in order to push the
material along the trough. Vibrating conveyor working member is trough, the trough is reciprocated to convey disposed therein
Materials. Pneumatic conveying equipment, hydraulic conveying device and the container-type devices to piped gas or liquid as the medium in the pipeline transportation of
materials.
Most uses electric drive conveyor, there is also an internal combustion engine driven, pneumatic or hydraulic driven.
The main parameters are generally based on the requirements of material handling systems, material handling location of a variety of conditions, the production process and
material characteristics to determine the main parameters. ① Transmission capacity: conveyor transport capacity per unit time is the amount of material transported. In transport bulk materials, transportation of materials per hour mass or volume calculations; during transportation into items, the number of pieces
per hour transport calculations. ② Conveyor speed: increase transmission speed can increase transmission capacity. In order to make conveyor belt retractor
Cited pieces and feed length is large, the conveying speed increasing day by day. But high-speed operation of the belt should pay attention to vibration, noise, and start
braking and other issues. For chains as traction element conveyor, conveyor speed should not be too large to prevent increased dynamic loads. Work simultaneously
Arts operated conveyors, conveyor speed production process requirements should be determined. ③ component size: scantling including conveyor belt width, belt width, hopper
volume, pipe diameter and vessel size. These have a direct impact scantlings conveyor conveying capacity. ④ lose
Delivery length and angle: transfer line length and inclination conveyor directly affect the size of the total resistance and the power required.
Development trend towards the development of the conveyor are: ① continue to large-scale development. Large transmission capacity, including large-scale, large single length
and large transmission angle and other aspects. Hydraulic conveyor length reached 440 km or more. Belt conveyor length of nearly 15 km single,
And has appeared composed by a number of Taiwan Contact B two places "belt conveyor path." Many countries are exploring long-distance, large-capacity transport of materials
better continuous conveyor structure. ② to expand the use of the conveyor. Developments in high temperature, low temperature, corrosive, radioactive
Sex, flammable substances in the work environment, as well as capable of delivering fiery, explosive, Pellet, sticky material conveyor. ③ the conveyor structure to meet the
automated material handling system to control stand-alone asked for. As used in automated sorting post office parcel trolley conveyor
Sorting machine should be able to meet the requirements of such action. ④ reduce energy consumption in order to save energy, the field of conveyor technology has become an
important aspect of research. Has one ton material handling energy consumed by one kilometer conveyor selection as one important indicator. ⑤ reduce all kinds of conveyors
Generated during operation of dust, noise and emissions.
Conveyor trends
Conveyor trends:
Chinese ancient high drum water overturned cars and mentioning, is the modern scraper bucket elevators and conveyors prototype; 17th century, began to apply ropeway transport
bulk materials; 19th century, the delivery of a variety of modern architecture machines have appeared.
In 1868, in the UK there has been belt; 1887, in the United States appeared screw conveyor; 1905, appeared in Switzerland steel Telescopic belt conveyor; 1906, in the United Kingdom and
Germany appeared inertia conveyor. Thereafter, conveyors manufactured by mechanical, electrical, chemical and metallurgical
Kim industrial technological progress, and constantly improve gradually from inside to complete the delivery of the workshop, developed to accomplish within the enterprise,
between enterprises and even between cities material handling, mechanized and automated material handling systems become an indispensable component.
Conveyor generally without pulling elements to be classified.
A conveyor having a traction member generally include traction, bearing components, drive means, tensioning means for redirecting means and the support parts. Tractor parts used
to pass traction, can be used conveyor, drag chain or rope; Holds material bearing member to have the hopper, bracket, or spreader
Etc.; drive to the conveyor to power, generally consists of motor, reducer and brake (stopper) and other components; tensioning devices generally have two kinds of screw and
hammer, pulling elements can maintain a certain degree of tension and vertical in order to ensure the normal operation of the conveyor; supporting member for supporting the
retractor
Cited documents or carrying member, can be idlers, rollers, etc.
A conveyor having a traction member structure is characterized by: the material to be transported to the traction member mounted on the bearing member are joined together, or in
directly mounted on the pulling element (such as belt), the pulling element or chain around both of the rollers connected to form load transportation of materials, including
branches and do not ship material
The no-load branch material, closed loop continuous motion using the traction member conveying materials.
Such a wide range of conveyors, the main belt conveyors, slat conveyors, trolley conveyors, escalators, moving walkways, scraper conveyor, buried scraper conveyor, bucket
conveyor, bucket elevator , overhead conveyors and overhead lifts and so on.
Conveyor without pulling element different structure and composition, working member for transporting the material is not the same. Their structure is characterized by: the use
of rotational movement of the work member or reciprocating motion, or by the medium flowing in a pipe conveying the material forward. For example, the roller conveyor
Machine working member of a series of rollers, the roller rotates to transport materials; screw conveyor working member of the spiral, spiral chute rotates in order to push the
material along the trough; vibrating conveyor working member of the trough , reciprocated chute placed therein to convey
The materials.
Conveyor will be toward the future large-scale development, to expand the scope, automatic sorting of materials, reduce energy consumption, reduce pollution and other aspects of
development.
Large transmission capacity, including large-scale, large single length and large transmission angle and other aspects. The length of the hydraulic conveyor belt has reached
more than 440 km length of nearly 15 km of single, and has appeared composed by a number of Taiwan Contact B two places "belt conveyor path." Many States
Home is exploring long-distance, large capacity continuous transport of materials conveyor structure better.
Extend the use of the conveyor:
In high temperature, low temperature corrosive, radioactive, flammable substances in the work environment, as well as capable of delivering fiery, explosive, agglomerate,
viscous material conveyor.
Expanding the use function of the conveyor
Conveyor can be heated and cooled, heat, squeezed, mixing, crushing and other functions.
Chinese ancient high drum water overturned cars and mentioning, is the modern scraper bucket elevators and conveyors prototype; 17th century, began to apply ropeway transport
bulk materials; 19th century, the delivery of a variety of modern architecture machines have appeared.
In 1868, in the UK there has been belt; 1887, in the United States appeared screw conveyor; 1905, appeared in Switzerland steel Telescopic belt conveyor; 1906, in the United Kingdom and
Germany appeared inertia conveyor. Thereafter, conveyors manufactured by mechanical, electrical, chemical and metallurgical
Kim industrial technological progress, and constantly improve gradually from inside to complete the delivery of the workshop, developed to accomplish within the enterprise,
between enterprises and even between cities material handling, mechanized and automated material handling systems become an indispensable component.
Conveyor generally without pulling elements to be classified.
A conveyor having a traction member generally include traction, bearing components, drive means, tensioning means for redirecting means and the support parts. Tractor parts used
to pass traction, can be used conveyor, drag chain or rope; Holds material bearing member to have the hopper, bracket, or spreader
Etc.; drive to the conveyor to power, generally consists of motor, reducer and brake (stopper) and other components; tensioning devices generally have two kinds of screw and
hammer, pulling elements can maintain a certain degree of tension and vertical in order to ensure the normal operation of the conveyor; supporting member for supporting the
retractor
Cited documents or carrying member, can be idlers, rollers, etc.
A conveyor having a traction member structure is characterized by: the material to be transported to the traction member mounted on the bearing member are joined together, or in
directly mounted on the pulling element (such as belt), the pulling element or chain around both of the rollers connected to form load transportation of materials, including
branches and do not ship material
The no-load branch material, closed loop continuous motion using the traction member conveying materials.
Such a wide range of conveyors, the main belt conveyors, slat conveyors, trolley conveyors, escalators, moving walkways, scraper conveyor, buried scraper conveyor, bucket
conveyor, bucket elevator , overhead conveyors and overhead lifts and so on.
Conveyor without pulling element different structure and composition, working member for transporting the material is not the same. Their structure is characterized by: the use
of rotational movement of the work member or reciprocating motion, or by the medium flowing in a pipe conveying the material forward. For example, the roller conveyor
Machine working member of a series of rollers, the roller rotates to transport materials; screw conveyor working member of the spiral, spiral chute rotates in order to push the
material along the trough; vibrating conveyor working member of the trough , reciprocated chute placed therein to convey
The materials.
Conveyor will be toward the future large-scale development, to expand the scope, automatic sorting of materials, reduce energy consumption, reduce pollution and other aspects of
development.
Large transmission capacity, including large-scale, large single length and large transmission angle and other aspects. The length of the hydraulic conveyor belt has reached
more than 440 km length of nearly 15 km of single, and has appeared composed by a number of Taiwan Contact B two places "belt conveyor path." Many States
Home is exploring long-distance, large capacity continuous transport of materials conveyor structure better.
Extend the use of the conveyor:
In high temperature, low temperature corrosive, radioactive, flammable substances in the work environment, as well as capable of delivering fiery, explosive, agglomerate,
viscous material conveyor.
Expanding the use function of the conveyor
Conveyor can be heated and cooled, heat, squeezed, mixing, crushing and other functions.
2013年7月28日星期日
How conveyor dust generated during the operation of the control
Bulk solid materials handling and processing are likely to generate and emit dust. There are places prone to dust feeding point, unloading points and material free fall zone.
Such as pneumatic conveying, hoist end, industrial belt conveyor transfer points, chutes and silos, etc. will generate dust.
Environmental protection and worker health protection laws are particularly heavy emphasis on control dust emitted playing, especially when dealing with potentially hazardous
(ie, toxic or explosive) materials must prevent dust emanating from the processing unit.
Dust explosion and health hazards are the two most important issues. Therefore, in the transportation of solid materials must be considered its harmful consequences and
prevention methods. Even a non-burning, non-toxic dust, when a sufficient concentration to the atmosphere should also be considered a nuisance. And
And extremely fine dust, if a sufficiently high concentration distribution in the atmosphere, there may cause mechanical failure of the device.
Dust control or air purification method and the nature of the solid particles include particles of mass, size and electrical properties, and made of the separation process.
In any particular application, the removal device selection by many factors, such as bulk solid material content, particle size range, the required collection efficiency and
ability operating costs. Generally the finer dust removal system corresponding to the higher costs.
In the dust control, it is important material properties are as follows: particle size distribution, moisture absorption, explosive, toxic, corrosive and electrostatic
properties.
The main purpose of dust control dust concentration is to be reduced to the extent permitted under - like the dust removal equipment and air purification equipment installed in
the operating system's various dust emission points. The best precaution is to dust removal equipment and production machinery and equipment interlocks, dust or air purification
equipment
Power transmission equipment, the production Airport conveyor of machinery and equipment to open.
There are various dust removal equipment, usually used in the following five ways: sedimentation; centrifugation; filtration; scrubbing; electrodeposition method.
Deposition techniques are generally applicable to large dust particles or as a primary purification. Large-diameter cyclone separator, a single, efficient, and also has a small
diameter, a plurality of combinations of the high efficiency cyclone. Fiber fabric filters, wet scrubbers and electrostatic precipitators can be used to control the fine dust
Dissipation and has high collection efficiency.
On the conveyor chain
Widely used in conveyor chains run as the lead member. In the fourth chapter describes the various upgrade Pipe conveyor in addition skip hoists are outside the rest of the chain as
a carrier member. Conveyor chain Optional requirements: Chain weight should be as light as possible, but the tensile strength should be large; better
Abrasion resistance; have good impact resistance; sliding and rolling resistance is smaller; easy assembly, fitting easily obtained; chain conveyors for special requirements to
high temperature and corrosion resistant.
Chains can be used to direct transportation of materials can also be installed on the chain attachment by pushing, pulling, scraping and other actions transportation of
materials. Because different types of accessories, in tandem with different transportation methods, resulting in different names conveyor. As the cost of higher chain conveyor,
maintenance costs
Also higher, nearly 30 years in the industrial applications gradually reduced. Chain conveyor can be used as high-quality, affordable design will still be taken seriously and
used.
Chain sliding and rolling of the points, Fang Wu transportation of materials can be carried slip me. Since the choice of the chain conveyor types and transportation of materials
in different ways and have different patterns.
Chain-slip transport mechanism made simple, small parts, relatively low cost, impact resistance, suitable for transporting rough, dirty, and materials containing sand. As the
chain slides on the track, the resistance and the friction is large, increasing the work of the chain tension. Because
This sliding of the chain conveyor drive power than necessary rolling of the chain conveyor is high.
Rolling machine and the input of the chain sliding chain conveyor, the former is smoother in the transportation of materials, friction is small, the required drive power is low.
In order to ensure the life of the wheel, the chain is not suitable for this type of rough, dirty, the output of the material containing fine sand
Send.
a carrier member. Conveyor chain Optional requirements: Chain weight should be as light as possible, but the tensile strength should be large; better
Abrasion resistance; have good impact resistance; sliding and rolling resistance is smaller; easy assembly, fitting easily obtained; chain conveyors for special requirements to
high temperature and corrosion resistant.
Chains can be used to direct transportation of materials can also be installed on the chain attachment by pushing, pulling, scraping and other actions transportation of
materials. Because different types of accessories, in tandem with different transportation methods, resulting in different names conveyor. As the cost of higher chain conveyor,
maintenance costs
Also higher, nearly 30 years in the industrial applications gradually reduced. Chain conveyor can be used as high-quality, affordable design will still be taken seriously and
used.
Chain sliding and rolling of the points, Fang Wu transportation of materials can be carried slip me. Since the choice of the chain conveyor types and transportation of materials
in different ways and have different patterns.
Chain-slip transport mechanism made simple, small parts, relatively low cost, impact resistance, suitable for transporting rough, dirty, and materials containing sand. As the
chain slides on the track, the resistance and the friction is large, increasing the work of the chain tension. Because
This sliding of the chain conveyor drive power than necessary rolling of the chain conveyor is high.
Rolling machine and the input of the chain sliding chain conveyor, the former is smoother in the transportation of materials, friction is small, the required drive power is low.
In order to ensure the life of the wheel, the chain is not suitable for this type of rough, dirty, the output of the material containing fine sand
Send.
2013年7月26日星期五
Vibrating conveyor of general and special purpose
Vibrating conveyor for general purpose
Vibrating conveyor and general material handling equipment is the main difference: the material on the conveyor vibration during transport is in "active" state, the carrier
member independence movement and the material does not move forward together; Other transportation equipment such as conveyor, the material in the transportation process is
"stationary
", And the bearing member is moving This important feature plus many other unique advantages, so that the vibration conveyor can solve many difficult material handling problems.
Although the vibrating conveyor can transport a wide range of material types, but with the particulate material transported over the transport material ground powder; conveying
flat or irregular spherical shape of the material than the material transport is good. With a Plastic belt conveyor to transport the material gas can be difficult; delivery
Density of the material, often due to air resistance of the material impact of the particle trajectories throwing, transportation would be in trouble. In addition, the fragility
of the material (such as milk powder and instant coffee granules, etc.) should be transported slowly, so as not to appear too much fragmentation. For conveying highly abrasive
materials
Material, because the material and conveying bottom surface contact time is very short, not bring much difficulty, in any case of wear-resistant lining of the tank to be easily
assembled.
While vibrating conveyor is mainly used for horizontal (or nearly horizontal) transport of fine-grained bulk solids or particulate Division. But can also be used for vertical
transportation of materials. Inclined upward transport within the range of about 15 degrees in most cases is possible.
Vibrating conveyor for special purposes
Most of the material conveyor only as moving from one place to another conveying device, while the advantage of vibrating conveyors transport the material in the screening
process can also simultaneously, dehydration, cooling or drying process operations. Conveying materials in order to prevent spilling and pollution, the conveyor
Tank on additional closures. When a clean and sanitary requirements of the occasion, the trough can be plastic or stainless steel.
For applications with multiple feed opening of the system, using a suitable opening and closing gates to control the export of material flow. Feed opening can be arranged along
the longitudinal direction of the conveyor, the conveyor can also be designed to split the one feed inlet stream into two or more strands.
In the vibrating conveyor trough the material being transported will be separated or mixed, and sometimes a good pre-blended material in the vibrating conveyor has been
extremely troublesome layered, but from another perspective, this phenomenon is also provided a simple and effective way to remove impurities from the product approach.
For example, using this method can be separated out unwanted upper materials. For some iron impurities can be separated by means of a solenoid system is easily removed.
An easier way is to work with a variety of screening process combines vibrating conveyor, for example, can use this method to remove the bulk material, you can also remove very
fine particulate material. The use of vibration as a forward mechanical transport of materials have been developed many very perfect series devices.
The gas or liquid in contact with the material being transported may be of a design appropriate to complete the groove by vibration, for example, by opening the side or bottom
of the tank to achieve; with a hot or cold air heat easily achieved or cooling materials; principle can also be direct wash water is transported
Materials.
The material to be transported can be cooled or dried. The structure has a double groove bearing surface can heat the gas chamber, when the conveying damp or wet materials, may
pass into the hot air chamber to prevent sticking tank volume materials. When at room temperature, the material for transporting frozen, the cold air can be introduced into the
gas chamber
Cooling tank surface.
Vibrating conveyor vibration facilities methods
The bulk solid materials vibrating hopper and unloading hopper to the
stored materials. Provide vibration method may be hit with a heavy
hammer to simply hit the side wall of
the hopper, or oscillating device with complex activator end positions. Vibration frequency can be 14 ~ 1300Hz, amplitude from near zero to large
At 60mm.
Vibration that can discharge capacity and material transmitted vibration reduction due to vibration of the bulk solid material strength. If the material is stored in an airtight
container, low-frequency vibration will make the material more dense; frequency vibration may cause the material may also lead to material bulk density, which is
And the corresponding amplitude of the nature of the material. It should be noted that, in the flow of the material required by vibration of occasions when the portable conveyor hopper
discharge port vibrations must not be closed. This results because of the material in any form will arch strength increases.
The hopper or bulk solid materials provide effective vibration There are two basic methods, namely silo wall vibrations and vibrations are directly stored materials.
Warehouse wall vibration
Hopper wall vibration is generally compressed air or by using the external hopper wall mounted electric vibrator to vibrate. A pneumatic piston vibrator type, electromagnetic
type and the eccentric rotary type (electrical or pneumatic operation).
Pneumatic piston vibrators rapping hammer with the outer surface of the hopper; electromagnetic vibrator has a similar effect, both the wall perpendicular to the vibration
bucket; eccentric rotary vibrator is Belt conveyor a vibrating device more expensive, generally life than short, compared with other types of vibrators, the need to stay low
Amplitude, high frequency operation, this device can be successfully used to move the material difficult.
Vibrator To properly placed in a position to produce the best results; selected amplitude and frequency of vibration must be sufficient to destroy the material arch. Under
normal circumstances, only be determined by experiment, usually affecting factors vibrator summarized as follows:
Type. About amplitude and frequency selection has some experience and law: that is, for raw materials, the general should adopt the low-frequency, high amplitude; For fine
powdery material is just the opposite. The specification shall be suitable hopper vibrator beveled plate rigidity and size.
Installation. Recommended hopper vibrator mounted on a steel reinforcing plate slope, and storage of the material as much as possible to increase the contact surface. Its
location in the "center of pressure" surface.
Vibration force. In most practical applications, the force necessary to apply part of the material silo cone weight of 1/10. If the density of the material is greater than
1440kg, the applied force is the weight of the cone part of the material 1/7; if the material density greater than 1920kg, the applied force is funnel portion was
Material weight of 1/5.
the hopper, or oscillating device with complex activator end positions. Vibration frequency can be 14 ~ 1300Hz, amplitude from near zero to large
At 60mm.
Vibration that can discharge capacity and material transmitted vibration reduction due to vibration of the bulk solid material strength. If the material is stored in an airtight
container, low-frequency vibration will make the material more dense; frequency vibration may cause the material may also lead to material bulk density, which is
And the corresponding amplitude of the nature of the material. It should be noted that, in the flow of the material required by vibration of occasions when the portable conveyor hopper
discharge port vibrations must not be closed. This results because of the material in any form will arch strength increases.
The hopper or bulk solid materials provide effective vibration There are two basic methods, namely silo wall vibrations and vibrations are directly stored materials.
Warehouse wall vibration
Hopper wall vibration is generally compressed air or by using the external hopper wall mounted electric vibrator to vibrate. A pneumatic piston vibrator type, electromagnetic
type and the eccentric rotary type (electrical or pneumatic operation).
Pneumatic piston vibrators rapping hammer with the outer surface of the hopper; electromagnetic vibrator has a similar effect, both the wall perpendicular to the vibration
bucket; eccentric rotary vibrator is Belt conveyor a vibrating device more expensive, generally life than short, compared with other types of vibrators, the need to stay low
Amplitude, high frequency operation, this device can be successfully used to move the material difficult.
Vibrator To properly placed in a position to produce the best results; selected amplitude and frequency of vibration must be sufficient to destroy the material arch. Under
normal circumstances, only be determined by experiment, usually affecting factors vibrator summarized as follows:
Type. About amplitude and frequency selection has some experience and law: that is, for raw materials, the general should adopt the low-frequency, high amplitude; For fine
powdery material is just the opposite. The specification shall be suitable hopper vibrator beveled plate rigidity and size.
Installation. Recommended hopper vibrator mounted on a steel reinforcing plate slope, and storage of the material as much as possible to increase the contact surface. Its
location in the "center of pressure" surface.
Vibration force. In most practical applications, the force necessary to apply part of the material silo cone weight of 1/10. If the density of the material is greater than
1440kg, the applied force is the weight of the cone part of the material 1/7; if the material density greater than 1920kg, the applied force is funnel portion was
Material weight of 1/5.
2013年7月25日星期四
Conveyor trough is designed to focus the content considerations
Air delivery slot design key consideration reads: air trough inclination; conveyors distance; conveyor trough width; need air; conveying material changes in direction; material
flow control; material bed surface air flow rate (in closed type air transport tank); power consumption
Consumption.
(1) the inclination of the air trough
Inclination of the trough according to the following main factors:
a. material fluidization characteristics. Fluidization characteristics determine the material trough must have a minimum inclination, may be the most important thing is the
material of the minimum fluidization air flow. When the minimum flow rate of a particular tilt angle (refer to the lowest air flow rate in practice), less than
This material does not flow forward tilt angle, unless and then increase air flow. In exchange for the higher air flow angle smaller, depending on the type of material and the
benefits obtained. It should be remembered that increasing the air flow will inevitably lose some of the benefits of the small tilt angle.
b. material inflatable extent and starting speed. If the material from a hopper or container, adding fluidization air trough, this material has the initial velocity, the speed
depends on the material of the gap size. The speed can not carry material along the ventilation chute moves a certain distance, the slip
Slot inclination angle than the natural angle of repose of material smaller. Moving distance on the starting speed, the tilt angle and the material nature of the difference
between the angle of repose of the material and in such conditions lose its fluidization velocity of the air.
Initial velocity of the flow of material on the Turn conveyor trough similar effect on a slight increase in the flow of air vent plate. If the feed is pre-fluidization, then for a
short trough can be beneficial, but the benefits of the long spout is too small.
c. hole plate breathability. The pressure drop of the air hole plate slightly larger than the air pressure drop across the board material layers. If the air pressure drop
through the vent panel is less than the pressure drop through the material layer is not sufficient to make the material completely fluidized, so we must increase the inclination
of the trough in order to obtain the
Required material flow.
d. the material flow. Increasing the inclination of the flow of material can be increased. In certain circumstances, the inclination of the trough increases from 4% to 6%, the
amount of air introduced into the same, the material flow can be increased to twice as much.
(2) changes in the transport direction
Fluidized material during transportation can turn downward or angled feed point and the unloading conveyor trough and the distance between hole plate to determine the final
choice of the type of arrangement. Any design can be the direction of flow of air needed trough. Some change in direction can be taken
Curved with a large tank, but is generally limited to a fiber fabric trough hole plate, using the minimum radius is usually 2m. In fact, the trough is generally 0 to 90 degrees
to change the angle between the appropriate direction by means of a conveyor can be directly slipped into the required slot outlet disposed at an angle other
A conveyor trough entrance.
(3) material flow control
Strict control of the fluidization air trough the flow of material is very difficult and long-term proper operation of the accuracy can be obtained, but not easy to obtain
accuracy of less than 1% by weight of a stable stream. Air flowing through the closed material flow trough through baffles to regulate, in the design of the range
From within a small fraction of all traffic to flow regulation.
Intermittent operation of the air regulating valve installed trough shall discharge end of the Airport conveyor trough, which can be completely shut off the flow to ensure that the
final volume and left in the unloading spout regardless of the height on the bed. If the valve is disposed at a certain distance from the discharge point where the trough
discharged from the amount of material of the valve
After leaving the material bed height. Material bed height and the inclination of the trough, and the input air volume and the kinds of the material being processed, the two
together of fact does not ensure a uniform batch batch operation.
In continuous feeding operation must control the amount of material added to the trough to prevent adding too much material cause obstruction.
Conveyor system analysis and design of the basic steps
Basic analysis of system design
The basic system design analysis include the following: to establish the system design goals, set the volume of transportation of materials, transport distance, material
processing methods, and to consider the future development requirements; collection of data about the material being transported, including fragmentation, bulk density and other
factors affecting treatment
Methods of characterization data; research available both inside and outside the factory floor space, attention may affect the types of roller conveyor systems or equipment
specification limit; study other site conditions and data: climatic conditions and public transport modes (rail, road and water transport, etc.); research plant energy, like
Compressed air, electricity, steam and gas and other supplies; research on past experience or a similar design system data; examine whether the material is sent to the
manufacturer's laboratory to test the necessity (for example pneumatic conveying system to carry the new material ).
The main steps of engineering design
From the above described method for engineering design can understand the concept of bulk solid material handling system design and analysis procedures should be designed. In
recent years, due to energy issues and the industry continues to progress, many engineering design company added a bulk solid materials transportation engineering
Department, the use of highly experienced engineers and technicians responsible for the whole system design work. Choose the world's most advanced technology and equipment,
industrial belt conveyor system design for a reasonable arrangement; selection of equipment meet the stringent requirements; rational use of space not only the area, but also
To control investment and shorten the construction cycle. To achieve these objectives, the design phase must have reasonable working procedures, as well as cooperation with
other sectors.
During the design before work, should be equipped with all the necessary information. First, according to material properties and the process parameters to study the transport
methods, routes and throughput, storage methods and storage, raw material input and product output mode, and to consider the type of transportation and storage equipment, etc.
And so on. Meanwhile, the reference to the relevant standards and site conditions, such as the buyer's specifications to check the system design and equipment selection has
affected or omissions.
According to the above considerations and research engineer responsible for the design of various factors and parameters can be summarized to conduct feasibility studies,
technical and economic comparison. After assessment, preliminary design.
In the preliminary design process for the system equipment selection and equipment data specified by the manufacturer should pay particular attention to the selected device
performance To learn more, others such as ordering the case, delivery date, equipment investment and the impact of design on other sectors . If the device support structure
Or foundation problems, pollution or dust problems, operational control of the complex and so on, until harmonization so far. In the initial design process, to negotiate with
the seller repeatedly research, control the investment under the premise of constantly modify the design, until both sides are satisfied. Then
Preliminary design cost estimate. Including equipment installed capacity is estimated as well as other indirect costs required. A detailed description of the preparation of the
system.
After the above steps, from initial design to enter the detailed design stage. Detailed design has the following main tasks: engineering flowchart; equipment specifications;
Equipment List; system specification; system floorplan; equipment capacity table; cost estimates table; said operation control system
Ming.
These data will be sent to the relevant departments as other professional engineering design basis and reference, such as civil, electrical, instrument control, and equipment
design department, while the purchasing department in cooperation with the inquiry, procurement and other work. After completion of inquiry, post purchase inspection department.
Inquiry
You can preselect several (usually four to five selection is limited) company at the same time, and ultimately to the best person for the selection of objects, submit the buyer
and the competent department for approval.
2013年7月23日星期二
Feed bucket elevator rationality

Feed bucket elevator is the main one working process, feed is reasonable not only affect the performance of bucket elevators, but also after the sequence work (promotion and
discharge process) will have a ripple effect. Thus, studies and efforts to implement reasonable feed has very important significance.
Measure the feed bucket elevator is reasonable, in general, consider two aspects: First, fill factor; Second, feed resistance. As we all know, of course, is feeding resistance
as small as possible, and fill factor is Elevator conveyor not necessarily better. In the design and field operation hoist when it reasonable feed
, Is essentially filled with the appropriate coefficients, feed resistance.
1 filled with an appropriate coefficient
Fill factor is too small (too small bucket interior quantity) is a typical "big horse car" phenomenon; fill factor too big and are not economical, because it is possible to
enhance the machine and the unloading process will be a "backflow" . Thus, the meaning of the appropriate coefficient chain conveyor filled: each of the other components to work
Conditions (such as raising the belt tension, wheel diameter and speed, etc.), bucket seat loaded in the machine after upgrading the material can successfully discharged from
the discharge port without generating the maximum fill factor reflux.
Fill factor affecting many factors, but can be summed up in the following aspects:
(A) feeding method
For grain, oil, feed mill workshop of bucket elevator feed forward manner with feed, reverse feed and bi-feeding, choose which feeding method should consider speed. When
upgrading the speed and flow of material with the base material when the flow rate are relatively small, generally used in reverse into
Materials, bucket inside scoop on the part of the base material and then filled directly from the inlet part of the material, which is conducive to the improvement of fill
factor. If you upgrade the speed and flow of material with the base material when the flow rate is relatively large, the material impact on the larger bucket, reverse feed is
not
Affects only filled coefficient improved, and additionally increase the power consumption can be used in this case the forward feed. If you fill factor is not easy to achieve
the required value, the "yield" falters, then the feed can be bi-directional. It should be noted that grain, oil, feed mill workshop
The bucket elevator feeding method is likely by the process, process layout of the decision.
(2) internal friction coefficient and the bottom wheel speed
Bucket seat when loading the machine, in theory, the material surface conform to the pole, as the center of the logarithmic spiral composed of logarithmic spiral surface
equations. Calculation, mapping show that: the internal friction coefficient of the material which filled coefficient; bottom wheel speed is slow, the material inside the bucket
coefficient
.
(3) bucket shape
In practice, it was found that the shape of bucket filled with impact factor. To increase the fill factor, but also conducive to the discharge, regardless of what type of
bucket, their basic form are large mouth with small, low internal high outside, bottom radiate round (no sharp corners). For enhancing the lightweight materials such as Google
Shell, bran, etc., in order to drain away the bucket of feed air to facilitate the bucket bottom opening (about 2 ~ 5mm in diameter), which is perforated bucket.
(4) feed flow
Filled with feed flow coefficient affecting one of the determinants. Some hoist mounted at the inlet feed flapper, to adjust the feed inlet cross-sectional area; Some hoist is
equipped with a buffer feeding means for regulating the feed flow.
Above mentioned factors influence coefficient filled grouped into two categories: one for on-site operation of uncontrollable factors, such as feeding method determined by the
designer, was promoted internal friction coefficient depends on the material, the bottom wheel speed and head round the same speed; second category is the uncontrollable factors
that the job site
Reliance on manual adjustment to control the feed flow rate as described above. On-site operation, adjust feed rate to control fill factor of great significance.
2 The feed resistance factors
Feeding resistance factors are mainly the following two aspects.
(A) the resistance movement
Bucket seat while loading the machine while running, its resistance on the one hand the performance of the feed bucket materials and friction between the material and the
friction between the inner wall of the base, the friction between the material and the material; hand , is the driving force of the material bucket. They are both running in the
material bucket
Proportional to the distance.
(2) material impact on the bucket
When the reverse feed, there is a direct part of the material is filled into the bucket and going, so that the material is produced on the bucket wallop. If the speed of the
belt and the material to enhance the flow of material to the base when the flow rate of greater material impact on the bucket is also larger, feeding resistance increased
accordingly.
Conveyor Belt Conveyor Idler Analysis

Roller dysfunctional
An influencing factor dysfunctional roller
(1) roller manufacturing quality. Roller manufacturing problems mainly in the stiffness of the bearing seat belt is not enough, it is difficult to ensure accuracy of the idler
assembly, thereby constraining the roller operation flexibility.
(2) use of sealed lubrication and maintenance. Since the work environment is more severe Belt conveyor , generally site dust are large, bearing the seal forms flexibility for
running a great impact idlers, if seal is not good, it is easy to enter the dirt caused by roller bearings rotation is not flexible;
Also, if using the general bearing grease calcium base grease dries easily change color, you can not play a very good lubrication.
Idler running flexible approach
(A) in the manufacturing process of idlers guarantee the accuracy requirements, such as stamping bearing bore precision to achieve three, dimensional tolerances of the pipe
ends, concentricity and ovality must comply with GB, can not exceed the difference .
(2) sealed lubrication, in addition to manufacturing quality assurance, but to go with the better lubricating materials, such as using lithium grease, you can improve the
lubrication conditions, which prolong the service life of the roller is very necessary.
(3) using the radial ball bearing bearings, labyrinth seal plastic seal ring structure, both to ensure that the work roller reasonable force, and dust effects, resistance, and
easy assembly and disassembly, easy to maintain, effectively reduce the operating costs of the conveyor.
Cause slippage
The main reason is caused by skidding traction rollers reduce friction, overloaded or belt is jammed.
(1) roller damage, debris winding, burying materials and other reasons will not turn a lot of rollers, conveyor belts or fittings damaged by increased resistance to idlers,
conveyor serious deviation, such as excessive cargo were so excessive resistance caused by belt conveyor design belt slipping.
(2) belt use for some time due to plastic deformation and elongation, resulting in insufficient belt tension, friction and traction while reducing slippage.
(3) the conveyor belt and the drive roller contact surface immersed in mud, dust, friction coefficient declined sharply, thereby belt slippage.
Tape slippage prevention and treatment
(A) to strengthen the operation of conveyor management, control the amount of material to prohibit overloading operation. In addition, the normal use of slip protection device,
when the conveyor belt to slip through the sensor signals, automatic shutdown, ease of maintenance treatment.
(2) on a regular or timely adjustment of belt tension. Car-tensioning device configuration or vertical belt tensioning device, belt slippage may add weight to resolve. But
should not add too much so as not to be subjected to unnecessary excessive belt tension and reduce its useful life; the
Spiral conveyor tensioning device configuration, when the belt slip adjustable tensioning stroke to increase tension; For those open layout of the conveyor, encounter rain,
snow, weather easily slip, the best Configuring hydraulic tensioner. Hydraulic tensioning device has an automatic increase in tension
Force compensation function, but also has broken with automatic shutdown feature.
(3) measures taken to prevent water spray, adding the non-face with a sweeper, and enhance the operator's responsibility, timely removal of mud on the roller, material and other
debris.
2013年7月22日星期一
Belt and gear oil spill prevention and treatment

Prevention and treatment of belt
(A) the reasons for belt
(1) belt tension is insufficient.
(2) to use conveyor overrun serious aging.
(3) water-washed coal conveyor drop; iron and other bulk materials and jam or punch hit conveyor.
(4) conveyor belt joint quality does not meet the requirements.
(5) conveyor belt joint severely deformed or damaged; conveyor belt joints metal clamp damage.
(6) belt running or rack stuck.
(7) acting on the belt tensioning means excessive tension on the belt.
(Two) off with prevention and treatment
(A) meet the requirements of heavy duty conveyor replacement.
(2) belt of its operational life, should be replaced.
(3) strict control of water coal, bulk materials and iron given to the conveyor.
(4) remove the poor quality of the conveyor belt joint, reconnect the conveyor belt; replacement metal clips.
(5) an increase of offset roller and anti-bias protection device; belt deviation was found stuck in the rack should immediately stop processing.
(6) the tension of the tensioning device to adjust appropriate.
(7) belt after the accident occurred, the following steps can be taken to deal with:
① cleared off the conveyor belt at the float coal;
② with card board with a one-off live;
③ with rope locked off with the other end;
④ Loosen the tensioning device;
⑤ winch traction belt;
⑥ cut Qi belt breakage;
⑦ with a metal clamp, cold bonding or curing method to connect conveyor belt;
⑧ After commissioning, after confirmation, and then put into use.
Reducer oil spill prevention and treatment
(A) the reasons reducer oil spill
(1) shaft oil spill: Bearing and gear oil groove back within a block; felts and apron damage or aging, seal failure.
(2) bearing gland screw holes spills or bearing cap end and gearbox casing junction surface leakage: Bearing gland fastening screws or washers are not damaged.
(3) gear oil spill at the plane of the housing counterparts: Reducer housing counterparts plane deformation; counterpart bolt connections are not tight and would damage the
sealing gasket.
(4) reducer gearbox casing filling hole cover and junction surface leakage: filling hole cover screw is tightened; gasket is damaged; filling hole cover deformation.
(5) gearbox oil spill: reducer shell burst damage.
(Two) gearbox oil spill treatment
(1) dredge gear unit oil return groove in shaft installation block oil pan; felt and gasket replacement.
(2) bearing gland tightening screws, replace the damaged gasket.
(3) reducer shell counterparts at the use of oil and rubber mats, fastening bolts counterparts, to replace the sealant.
(4) the filling hole cover fastening screws, replace it.
Broken arch is in the coal bunker in the working principle and characteristics

Various types of coal bunker, hopper, coal, material stagnation in their positions in vivo blocked, put no, resulting in the production effects of the accident. Broken arch
device is to resolve this situation as a stagnation blocking equipment, installation bunker coal mining enterprises, through the production practice, indeed solve the stagnation
of coal in its warehouse in vivo
Blocking problem, to avoid affecting the production and use of safe and Flexible Roller Conveyor and efficient.
Ground coal mining enterprises, underground, coal washery and others have coal bunker. Due to wet coal bunker, large chunks of coal gangue in the series or for internal
bagging coal within the coal bunker untaken long backlog of stagnation knot together and form can not flow occlusion fault zones, coal bunker under the mouth do not put coal
feeder out of coal, vulgar
Said lag eye. This problem also plagued the production of coal mining enterprises, the traditional processing methods: artificial poke pound, pressure water jetting, explosives,
mechanical vibration. Its effect is poor and unsafe. Broken arch device (also known as air guns and blocking device) is to prevent and eliminate all types of coal bunker coal
bagging, sticky positions
, Blocking eye phenomena such special devices. When using blasting impact energy, no harm, no pollution, reduce labor intensity, to ensure safety in production, is an
economical, ideal security device attempts to prevent the eye.
A broken arch device works
Arch-breaking device is in mine air piping for air as the medium, the use of aerodynamic principles, its internal pressure devices and can realize automatic control of
quick exhaust valve, air pressure can be instantly transformed into air jet power can produce Suddenly a strong airflow Gravity roller conveyor directly into the bulk storage
Coal and other materials occlusion body faulty area, the expansion of such a sudden release of the shock wave, to overcome the static friction of the material, the material
within the container to restore flow again.
Two broken arch Features
Broken arch has a simple structure, easy installation, impact force, easy operation, continuous operation, no damage to the body such positions; jet burst quickly,
effectively destroy bagging, solve the congestion problem, is an ideal device attempts to prevent the eye.
Its use advantages: ① mute action, low noise, no pollution; no leakage design, efficient use of energy; does not compress within the coal bunker; ② minimum maintenance:
simple moving parts, no motor, no bearings, no lubrication; strong jet burst power, effective range
Wai Kwong; ③ spray piston reset immediately after the explosion to block dirty substance inside the silo into the broken arch playing devices; ④ long life, maintenance-free
within a year guns inside.
Of course, for large-scale coal bunker, using a combination of air guns, large force.
2013年7月21日星期日
Loaders and maintenance characteristics and apply
Loader Features
1 wear faster
Since the new machine parts processing, assembly and adjustment factors, the friction surface roughness, with the surface contact area is small, uneven surface pressure
conditions. The machine during operation, some parts of the surface irregularities friction fitted to each other, grinding down to the metal debris and continue to participate
as an abrasive friction, more accelerated wear of the mating surfaces of the parts. Therefore, run-in period is likely to cause parts (especially the mating surface) of the
wear, wear faster. At this time, if the loader overload operation, it may cause damage to components, resulting in premature failure.
(2) poor lubrication
Parts of the new assembly with the gap is small, and of the assembly and other reasons, it is difficult to ensure uniformity with the gap, lubricant (grease) on the friction
surface is not easy to form a uniform film to prevent wear. Thereby reducing the lubrication performance, resulting in abnormal wear of the early parts. Cause serious friction
with precision surface scratches or bite phenomenon, leading to failure.
3 loosening
New processing and assembly of parts, the presence of geometry and with the size of the deviation, the initial period, due to shock, vibration and alternating load, and heat,
deformation and other factors, coupled with excessive wear and other reasons, easy to make the original tightening of loose parts.
4 leakage occurs
Loosening of the mechanical vibration of combined heat the machine, the machine and the sealing surface fitting logout leakage phenomenon, part casting, machining and other
defects in the assembly debugging difficult to find, but during the operation of the vibration, shock role of this flaw is exposed, the performance of the drain (infiltration)
(water), therefore, prone to leakage run-in period.
Loader application and maintenance
1 Because of construction machinery is a special vehicle, operating personnel should receive factory training, guidance, and the machine structure, properties have a full
understanding and get some experience in the operation and maintenance before operating the machine. Manufacturers to provide "product maintenance manual" is the operator to
operate the equipment necessary information before operating the machine, be sure to read the "maintenance manual", according to the requirements of operation and maintenance.
2 Note that the run-in period workload, run-in period should not exceed half of the workload of 60% of the rated working load, and to arrange for appropriate workload, long
continuous operation to prevent the machine overheating caused by the occurrence of the scene.
3 Note that frequently observed instrumented, abnormal should be excluded promptly stop in reason is not found, the fault is not excluded should be stopped before operation.
4 Note that regular checks of lubricating oil, hydraulic oil, coolant, brake fluid and fuel oil (water) bit and the quality and attention to check the tightness of the machine.
Inspection found that too much water is missing, you should analyze the reasons. Meanwhile, the lubrication points should be strengthened lubrication is recommended run-in
period, the class must be on the portable conveyor lubrication point greasing (except for special requirements).
5 Keep the machine clean, adjust, tighten loose parts to prevent loosening due to increased wear and tear parts or cause parts missing.
6 run-in period is over, deal with the mandatory machine maintenance, inspection and adjustment of work to do, while paying attention to fluid replacement.Flat belt conveyor
On the belt deviation problems
A conveyor belt deviation meaning
Conveyor during operation, the conveyor belt center line from the centerline of one side, a phenomenon known as the belt deviation.
Second, the conveyor belt deviation hazards
When the conveyor belt deviation, causing friction between the belt edge and frame, so that premature belt edge damage, deviation serious, conveyor idlers and will fall off,
causing a major accident would not only affect the production, transport damage band, when using non-flame retardant conveyor belt, but also because of increased deviation
conveyor running resistance, so that belt slippage could cause mine fire accident. For example: When the conveyor belt deviation, ripstop protection device failure; serious
deviation, conveyor belt is stuck and slipping; rack if the deviation is jammed, broken belt accident prone.
Third, the reasons for deviation conveyor
Deviation of conveyor belts mainly due to discontinuity caused. Specifically the following situations:
(A) the tail drive pulley or drum two diameter sizes;
(2) rollers or roller surface slime or other attachments;
(3) the nose and tail drive pulley drum is not parallel;
(4) drive pulley, tail pulley shaft centerline is not perpendicular to the fuselage centerline;
(5) roller is improperly installed;
(6) Feeding malposition;
(7) roll center is not the center line of the fuselage;
(8) incorrect or conveyor belt joints on both sides of aging deterioration caused by deflection;
(9) Body errors (frame tube, H frame spiky);
(10) belt is too loose.
Fourth, the conveyor belt deviation prevention
1, install anti-deviation protection devices
To prevent tearing conveyor belt, currently mostly used conveyor-type anti-deviation limit switch protection device. It consists of anti-bias sensor and control box. When the
conveyor belt deviation, the conveyor belt toward the outside of the vertical roll, so that the sensor contact with the movable contact and the fixed contact. Through the
control box off conveyor downtime. General use stalk roll-limit switch on the conveyor belt deviation monitoring.
2, improve the quality of the installation
3, to improve the quality of conveyor belt joint
4, to strengthen inspection and maintenance tour
5, to ensure unbiased loading
6, to ensure the normal cleaning device
Caking coal cleaning the drum, you must first shut down, clean up later. Non-operational side edge cleanup. Prohibit scraping shovels and other tools on the conveyor belt or
tool slime positive deviation of dial belt to avoid injury.
2013年7月18日星期四
订阅:
博文 (Atom)